Hot Stamping Technology
Hot Press Forming
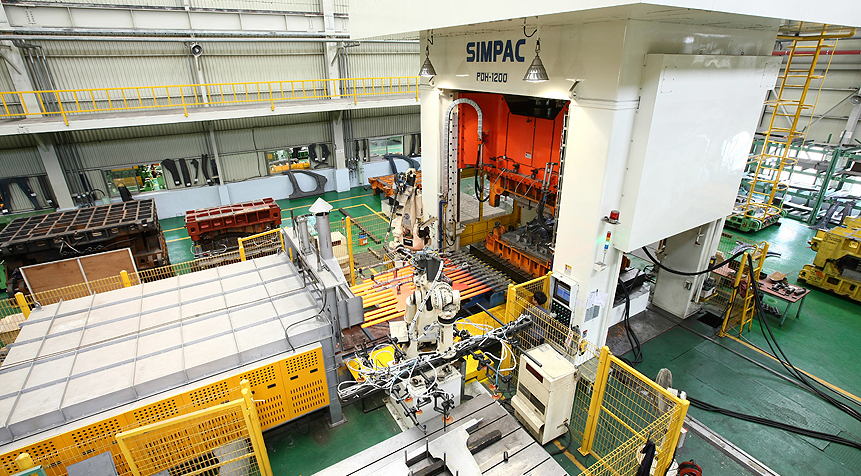
– Hot press forming is the method that press-forms the boron steel in high temperature. First, It's heated at 900 to 950℃,
then pressed and quenched in the die. The final strength reaches up to 1,500Mpa, 3 times higher than unprocessed steel.
With this technology, it is possible to obtain high strength with thinner plate.
– This technology brings weight lightening effect by 10-15% and minimizes the use of raw materials, which leads to cost
reduction effect.
Not Less than 700MPa
Die Production Development Process
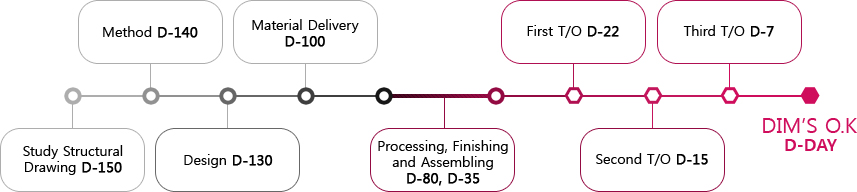
Technology
Production
REINF SIDE OTR Parts Integration
- The parts such as FRT PLR OTR , RAIL ROOF SIDE, CTR PLR OTR, and SIDE SILL OTR were produced in
multiple parts and welded into one part before. HPF casting technology is used to produce integrated part
instead of joined parts.
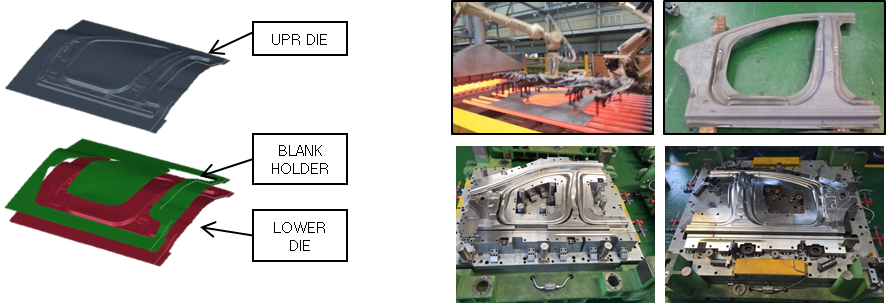
BEFORE 6 PART
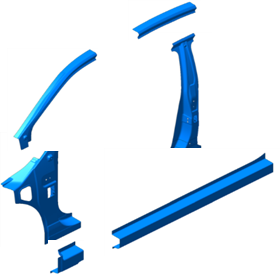
AFTER 1 PART
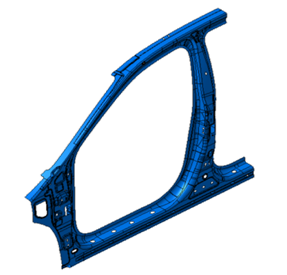
※ Weight reduction : 15%, Less assembly : 6 parts -> 1 part, Cost reduction : 20%
Local Softening Technology
1) TAILORED Molding
- Forming in the optimal strain shape with different tensile strengths by sections to protect passengers
on vehicle impact.
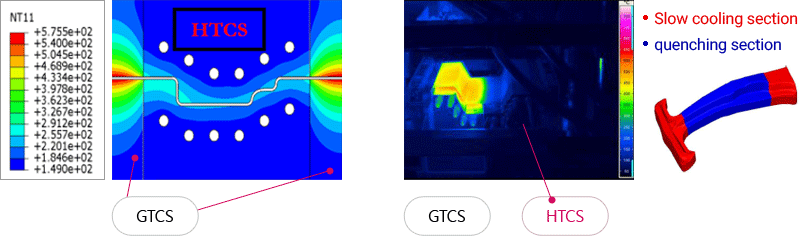
- Required of Die modeling that reflects coefficient differences of thermal expansion in materials.
2) Electric Heat Type Molding
- Modeling technology that differences in thermal expansion of the mold are considered for temperatures of
the quenching section and the slow cooling section.
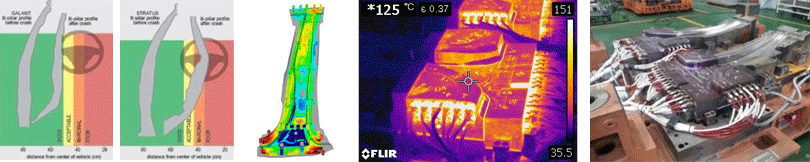
- Die materials and heater placement to control the mold temperature of the softening section
Hot Trim Die Technology
- Realized cost reduction by shortening the laser cutting time
- Trimming under the soft state before the material becomes hardened by cooling
- Trimming at the same time in the hot forming process without the separate die
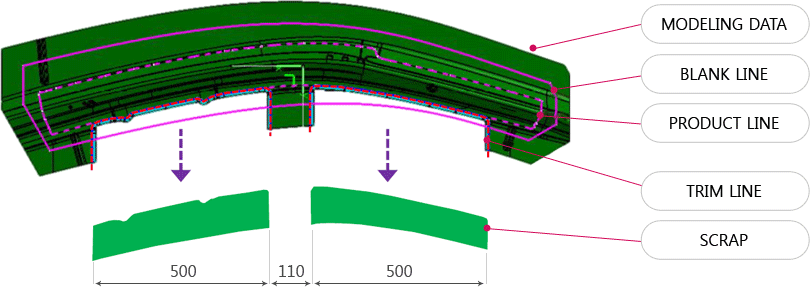
Cold Trim Die Technology
- Laser processing is replaced with press processing
- Establishment of the modeling standard that predicts the deformation of the die structure against
concentrated load and impact.
- Processing precision of each part is ensured by the 3D build up design, which eases repair replacement.
- Wear resistance, high hardness, easy heat treatment and welding property ensured for die materials.
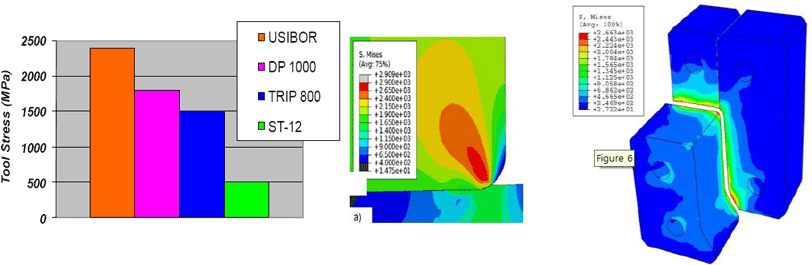
Technology
Direct Injection Water Cooling Technology
- Shortened cooling time to enhance part production cost
- Improved the cooling property of the section the cooling speed is lowered due to short of the surface
pressure due to reduction in the thickness of the wall material.
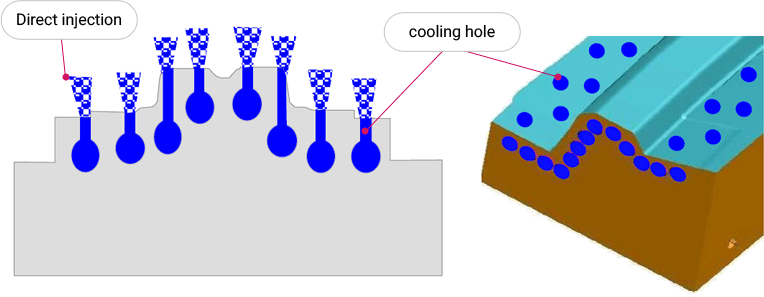
– Coolant Channel Based
Machining Method
Cooling Efficiency Improvement – Coolant Channel Based Machining Method
- Improved the steel treatment method to design the uniform cooling line on the shaping plane.
- Selection of the efficient treatment method for water tightness and the die maintenance
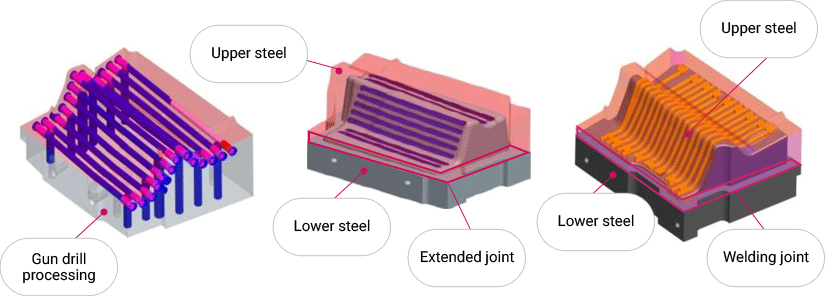
Hot Stamping Thermal Flow/Fluid Analysis
Hot Stamping Optimized cooling channel structure of the die for cooling efficiency increase
- Minimized generation of turbulence by vector analysis
- Optimized cooling channel design by analysis on the heat stagnation section
- Induction of the same temperature distribution for each channel.
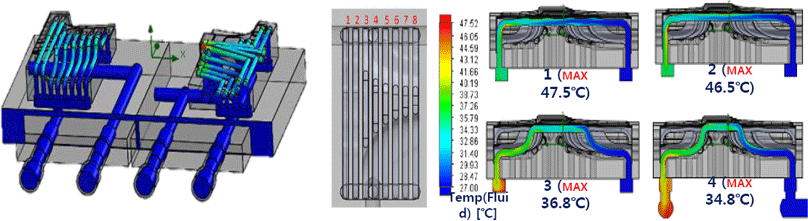
-
01
Die Design
(Design) -
02
Modeling
Simplification -
03
Lattice Forming
(Mesh) -
04
Properties and Boundary
Conditions
Setting - 05 Analysis
-
06
Analysis and
Design Modification